Products
We manufacture medium voltage switchgear (MVSG) and VFD, ODM/OEM is supported.
Let's Talk About Your Needs
Customized Solutions to Your Projects
We can offer customized solutions to your projects, just share your needs/requirements with us, and we will send 2D/3D drawings for confirmation before production. We can customize everything you want including but not limited to:
- Your Logo
- Panel Language
- Housing Size
- Circuit Breaker
- Load Switch
- Fuse
MV Switchgear Procurement: A Comprehensive Buyer's Guide
Chapter 1
What is a MV switchgear?
Chapter 2
What size is a medium voltage switchgear?
Chapter 3
MV switchgear components
Chapter 4
MV switchgear applications
Chapter 5
Types of MV switchgear
Chapter 6
Important tests for MV switchgear
Chapter 7
What is the IEC standard for MV switchgear testing?
Chapter 8
What is the difference between LV MV and HV switchgear?
Chapter 9
What is the life expectancy of a medium voltage switchgear?
Chapter 10
MV switchgear design guide
Chapter 11
MV switchgear training
Chapter 12
MV switchgear manufacturers
Chapter 1
What Is A MV Switchgear?
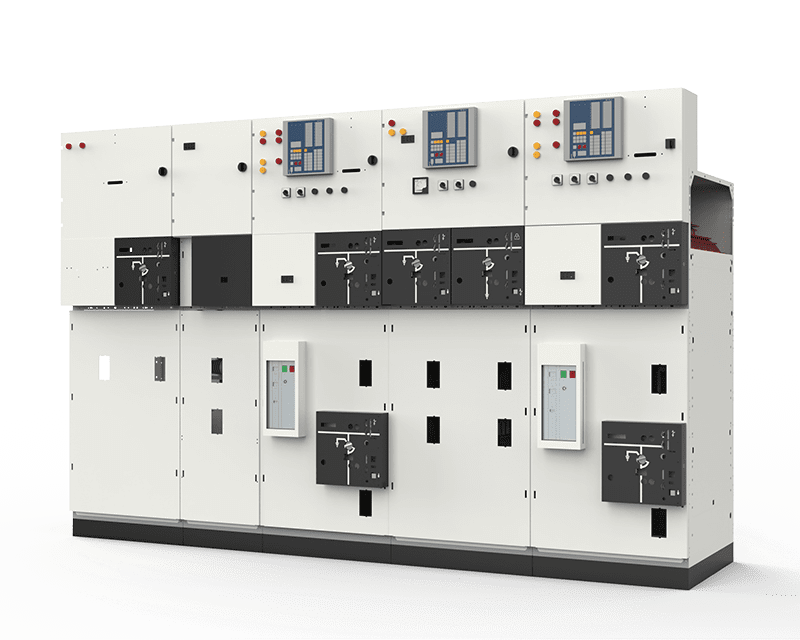
Medium Voltage (MV) switchgear is an important piece of equipment used to manage, protect, and control electrical power distribution in the range of 1 kV to 36 kV. MV switchgear is built to meet the stringent requirements of IEC 62271-200 and Tedaş MYD. It is used in both AC systems from 1 kV to 52 kV.
According to ANSI and IEEE standards, voltage classifications include low-voltage (up to 600V, expanded in NEC 2014 to include up to 1,000V), medium-voltage (600V to 69 kV), and high-voltage (69 kV to 230 kV). Medium-voltage switchgear is usually rated up to 36 kV, even though it can handle up to 52 kV, to match common power distribution practices.
Medium-voltage switchgear is the backbone for electrical control. It’s the thing that breaks the circuit, disconnects the circuit, fuses the circuit, or relays the circuit. It’s all contained in a big metal box. It’s what stops the current from flowing when it spikes, and it’s what stops the current from flowing when something shorts out.
The broad range of voltages is important because it means you can use MV switchgear in many different places. It keeps your power system running efficiently and safely in many different applications. You can switch things on and off with it, which is important because you need to control and isolate equipment to keep your electrical system working right.
Chapter 2
What Size Is A Medium Voltage Switchgear?
Medium voltage switchgear typically ranges from 1 kV to 36 kV. However, the physical dimensions can vary greatly depending on the specific type, manufacturer, and configuration. Generally, the size includes factors such as the number of panels, the types of components included (such as circuit breakers or disconnect switches), and the design (compact or standard).
Please find the dimensions below for the Russian market for your reference. IE-Supply can create customized sizes for your projects as needed.

These sizes are approximate and may vary depending on the design requirements, additional components needed, and safety considerations.
Chapter 3
MV Switchgear Components

Circuit Breakers: The most important part of switchgear is the circuit breaker. Circuit breakers interrupt the flow of electricity to keep it from damaging the system due to things like overcurrents, short circuits, and other electrical faults. Circuit breakers come in different types, including air, vacuum, and oil circuit breakers. They can be operated manually or automatically.
Fuses: Fuses are designed to protect the electrical system by breaking the circuit if the current exceeds safe levels. When the current becomes too high, a metal strip inside the fuse melts, which breaks the circuit and stops the excessive current flow.
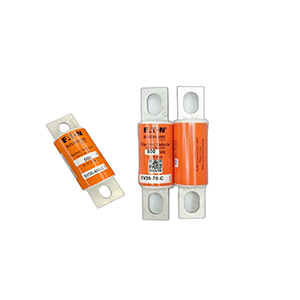
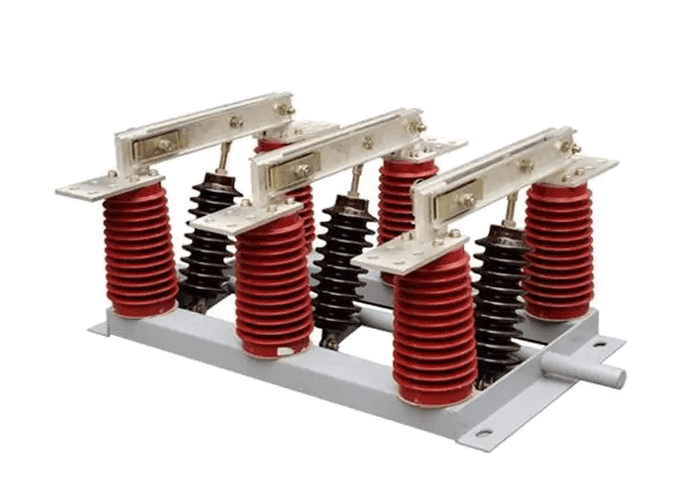
Disconnectors (Isolators): Disconnectors are used to isolate parts of the electrical system for maintenance or during faults. They ensure that the circuit is completely dead, so it’s safe for people to work on the equipment.
Relays: Relays are devices that monitor the system and detect faults. When they detect a fault, they trigger the activation of protective devices to keep the system safe and reliable.
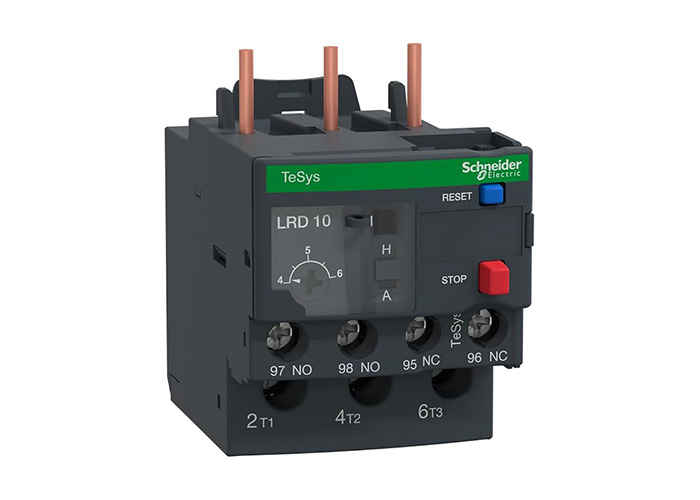
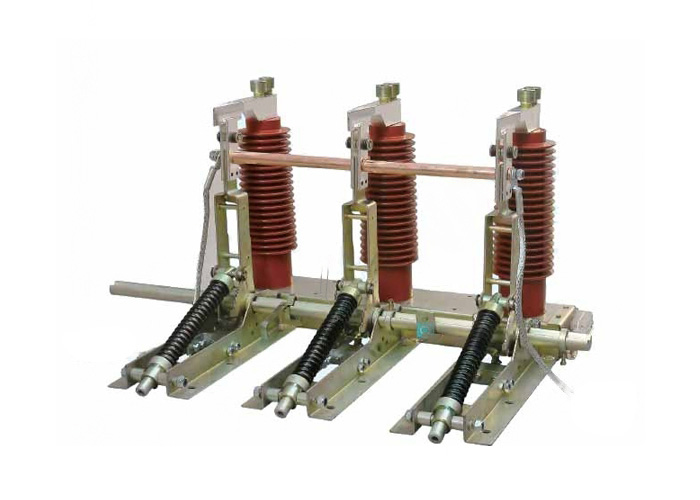
Grounding Switches: Grounding switches are used to connect the electrical equipment to the ground. This helps to dissipate any static electricity and provides a path for fault currents to flow, which makes the system safer.
Surge Arresters: These devices protect against voltage spikes that can damage equipment. They work by diverting excess voltage away from sensitive components and into the ground.
Instrument
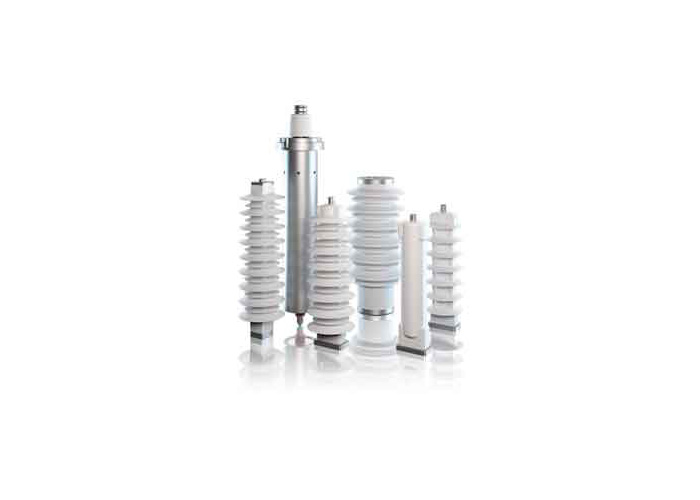
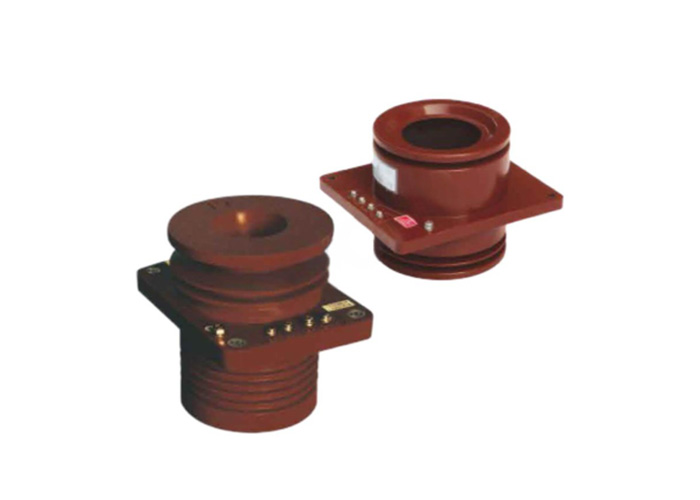
Transformers: These include current transformers (which reduce high currents to a lower, manageable level for meters or relays) and voltage transformers (which lower the voltage for measurement and protection purposes).
Auto Reclosers and Sectionalizers: Auto reclosers help restore power automatically after a fault is cleared, improving system reliability. Sectionalizers divide the network into segments, allowing targeted isolation of faults, which facilitates quicker repairs without extensive downtime.
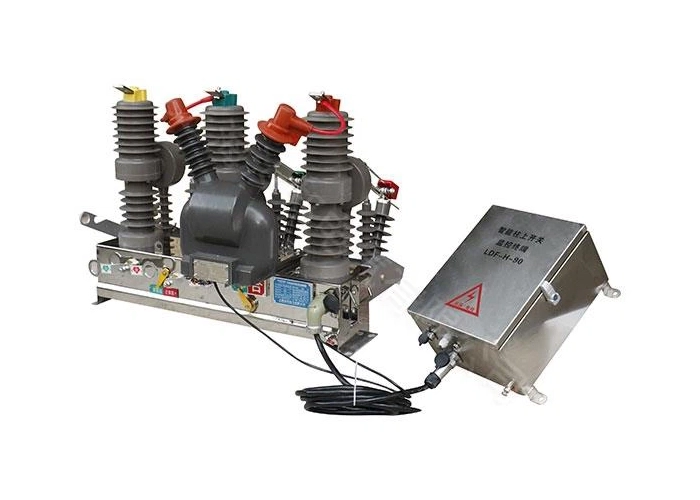
Each component within the MV switchgear has a specific role, from protection and isolation to fault detection and operational management, ensuring efficient and safe operation of medium voltage electrical distribution networks.
Chapter 4
MV Switchgear Applications
Medium Voltage (MV) switchgear is used in all industries that use medium voltage electricity. It is used in a wide variety of applications and is essential for electrical energy management and safety.
Power Distribution
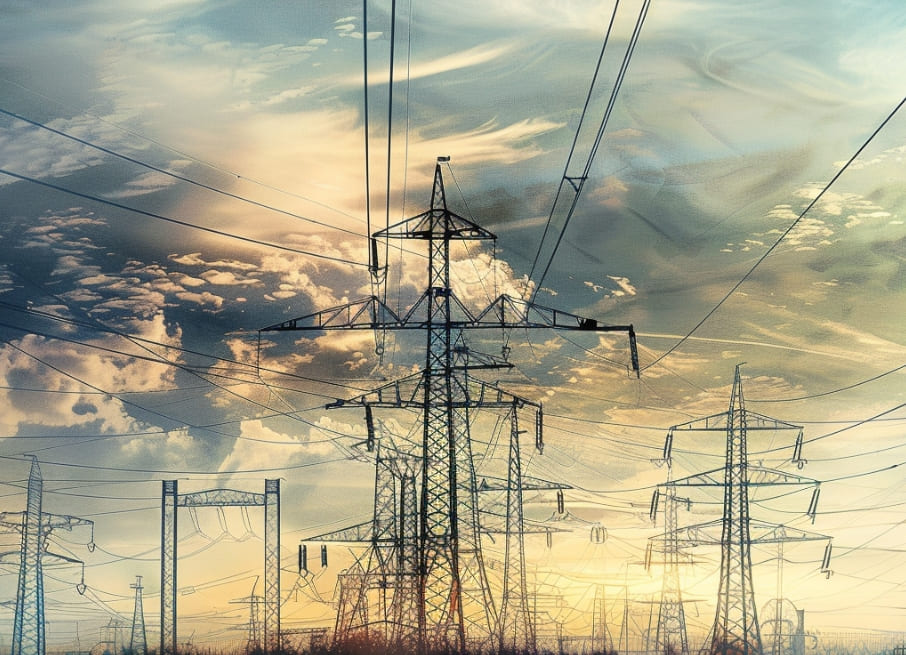
MV switchgear is used to distribute electrical power. It takes power from the high-voltage transmission lines and distributes it to the low-voltage distribution network. This is necessary to get power safely to the end user, whether that is a house, a building, or an industrial plant.
Industrial Applications
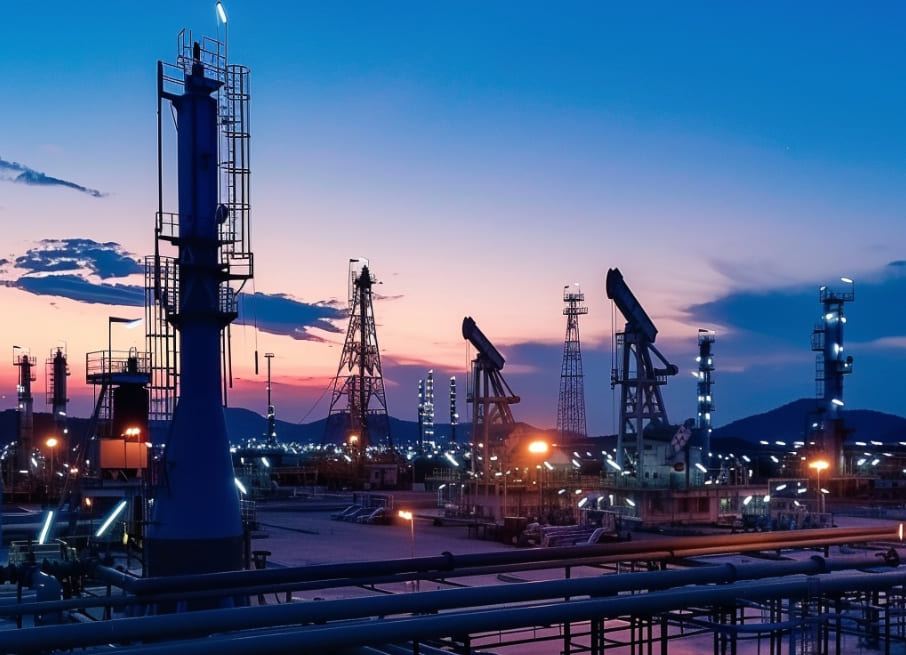
MV switchgear is also used in industry. Industries like mining, oil and gas, chemicals, and manufacturing have equipment that requires protection. It is important to be able to distribute power to that equipment safely and reliably. If there is a problem with the power distribution, it can cause the equipment to stop working or be damaged.
Renewable Energy Integration
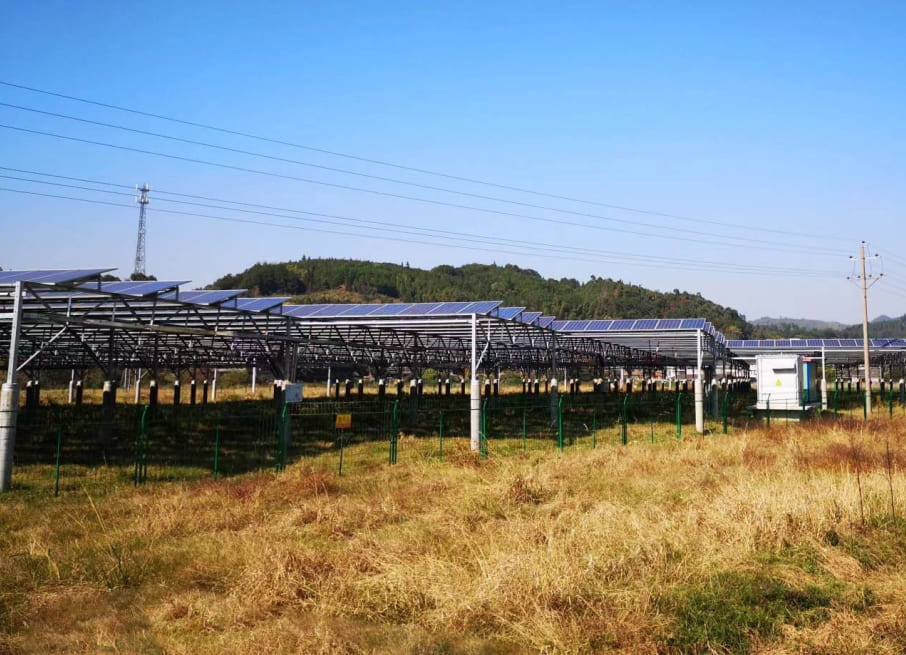
With the world’s focus on renewable energy, MV switchgear is critical to the integration of renewable energy sources into the existing power grid. It is used extensively in solar farms and wind turbines to manage and route the power generated to the grid. The switchgear ensures that the variable and sometimes unpredictable power from these sources is handled safely and efficiently, allowing renewable energy to be integrated into our daily energy consumption.
Infrastructure And Public Utilities
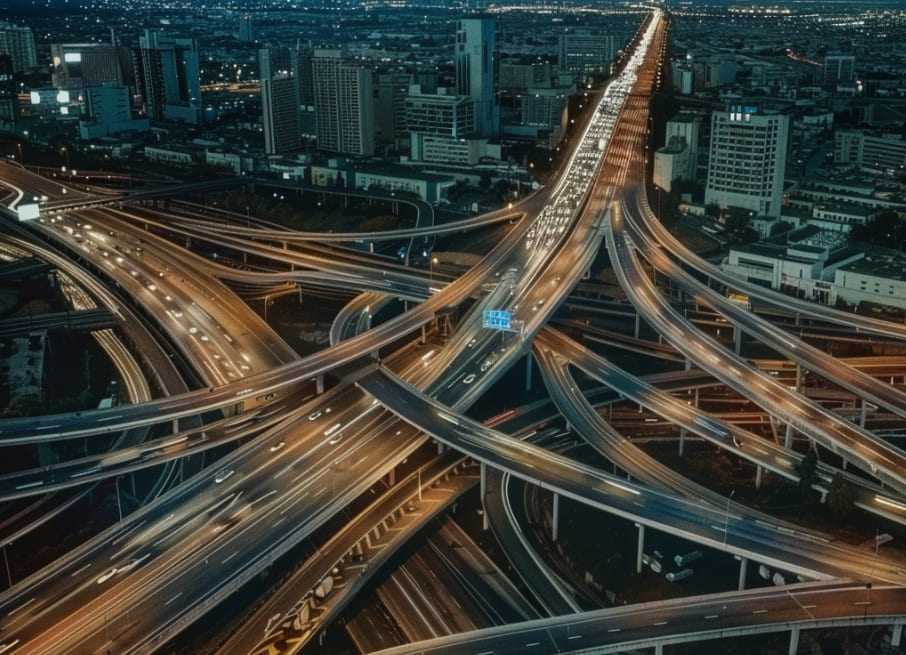
MV switchgear is also critical to the operation of hospitals, data centers, and rail systems, where reliable power is critical. It improves the reliability and resiliency of the electrical systems in these high-stakes environments. By serving such a wide range of industries, MV switchgear not only supports the backbone of modern power distribution systems, but also helps to increase the adoption of renewable energy technologies, making it a key player in the sustainable energy landscape.
Chapter 5
Types Of MV Switchgear
Lorem ipsum dolor sit amet, consectetur adipiscing elit. Ut elit tellus, luctus nec ullamcorper mattis, pulvinar dapibus leo.
Air-Insulated Switchgear (AIS)
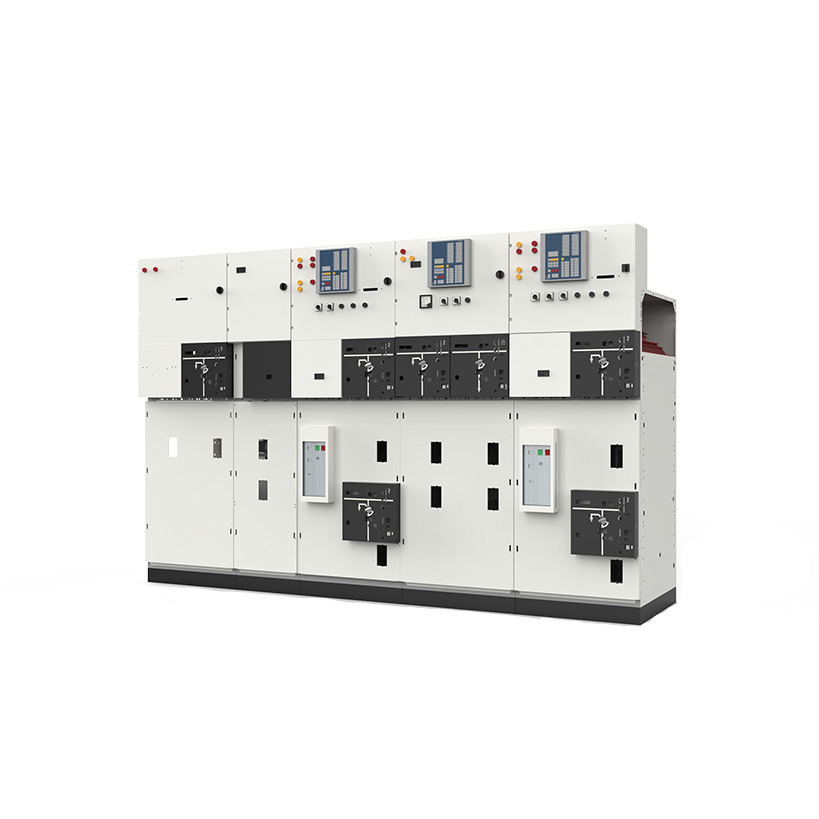
This is the most common type and uses air as the insulation medium. AIS is simple and reliable, but it usually requires more space because it’s so spread out.
Gas-Insulated Switchgear (GIS)
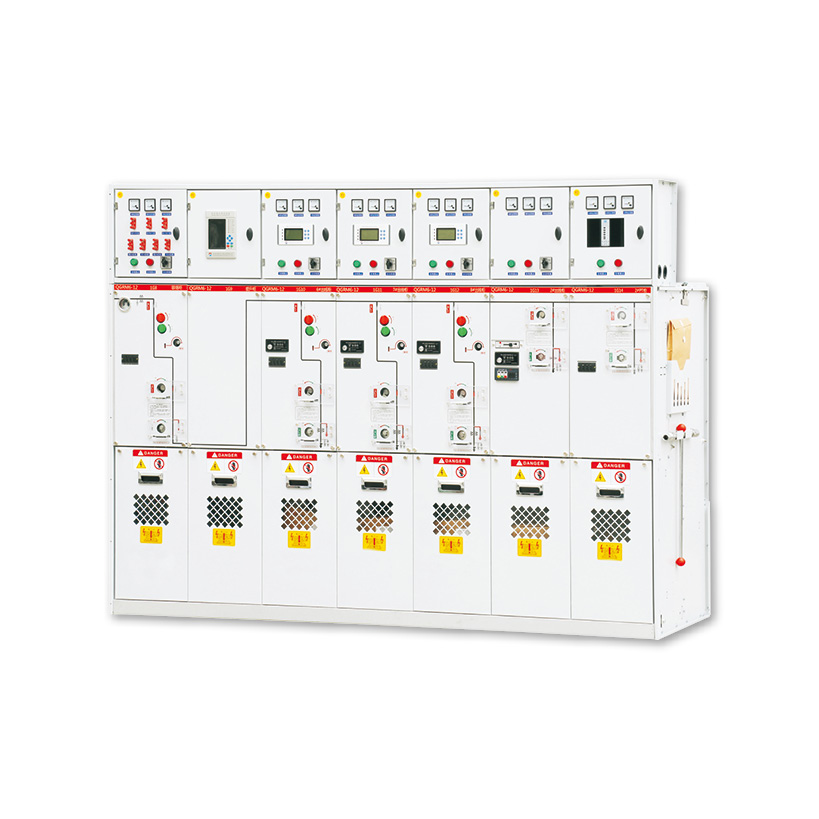
This type uses sulfur hexafluoride (SF6) gas for insulation, so it’s more compact and has better insulation properties. GIS is smaller and less sensitive to environmental conditions, but it’s usually more expensive and requires more maintenance.
Hybrid Switchgear
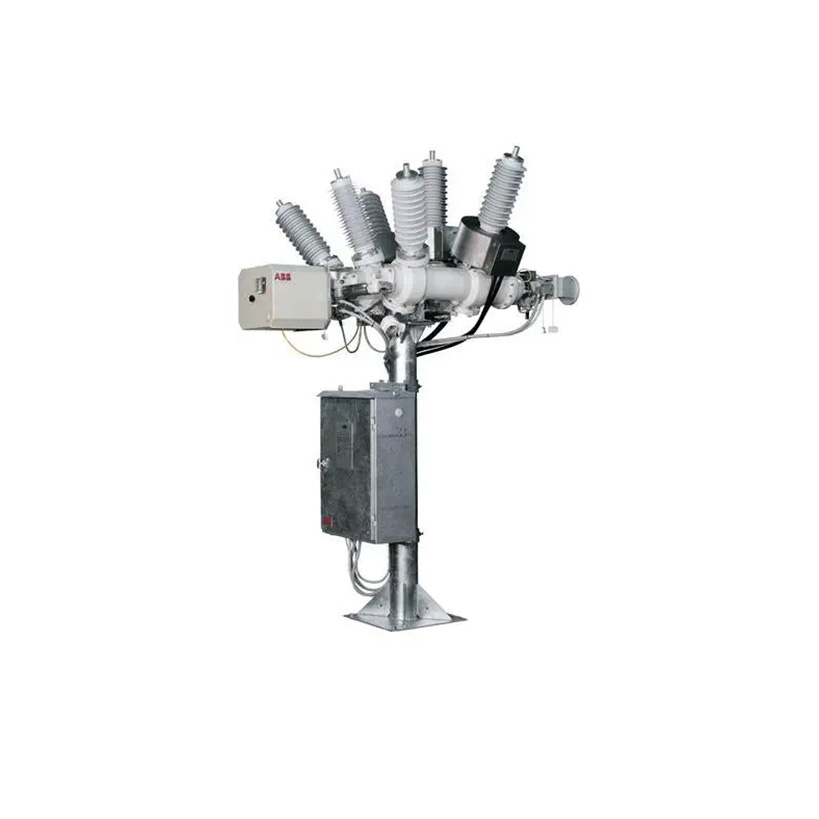
This type is a combination of AIS and GIS technology. It uses a mix of air and SF6 gas for insulation. Hybrid switchgear is a good balance of reliability and compact design and can be used in many different applications.
Compact Switchgear
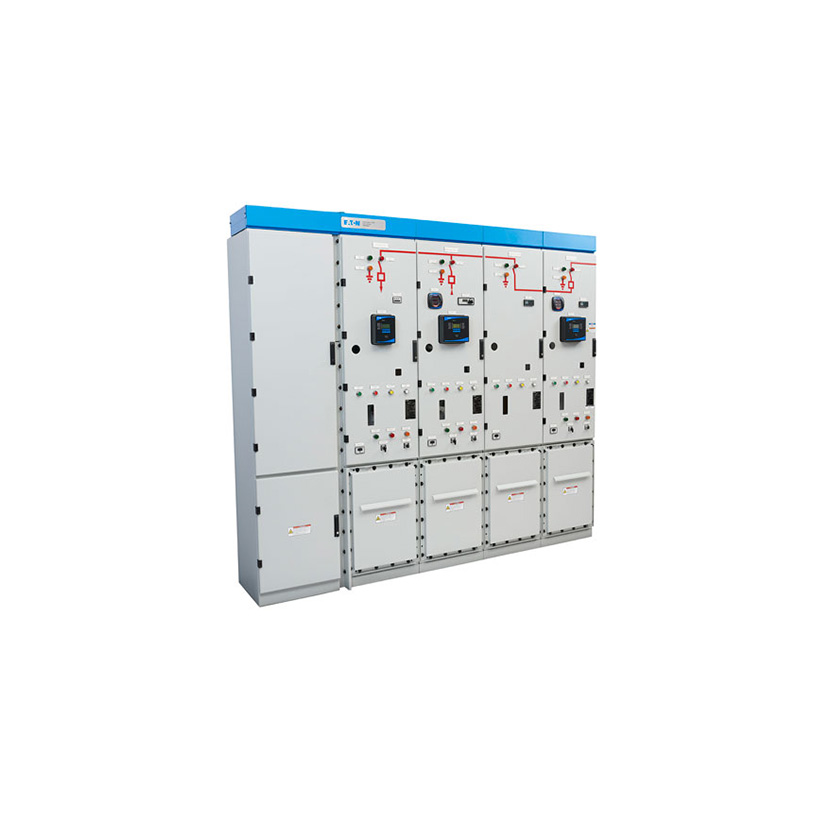
This is a small metal-enclosed solution with sealed circuit breakers and disconnects. It’s designed for areas where space or access is limited. It meets IEEE C37.20.9 and IEC 62271 performance standards.
Metal-Clad Switchgear
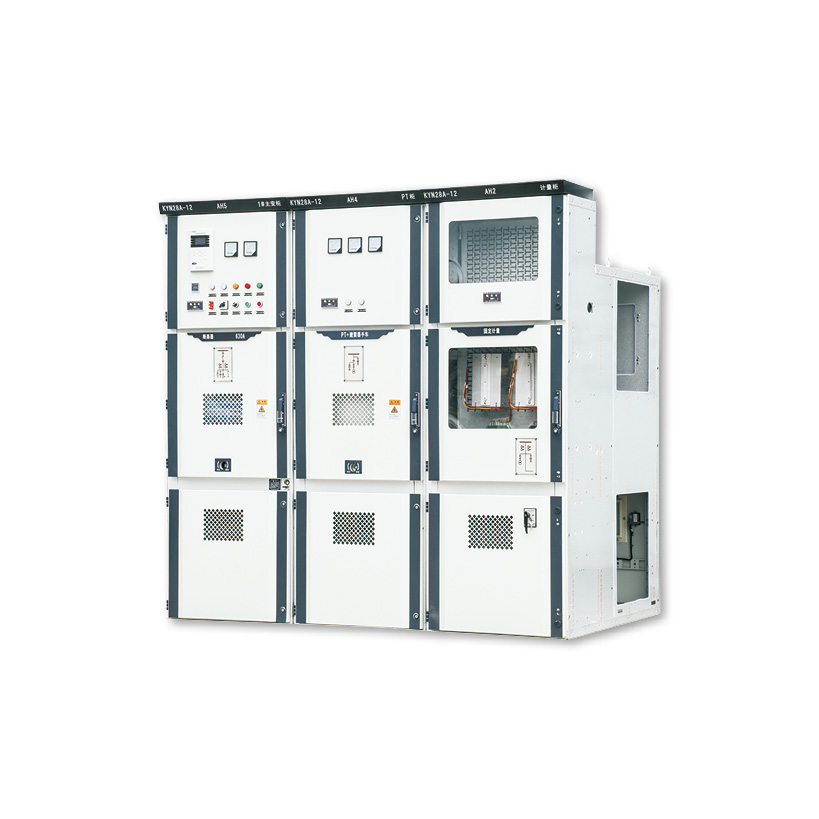
Defined by IEEE C37.20.2, this type of medium-voltage (MV) switchgear has separate metal compartments for each circuit breaker, increasing safety and making it easier to work on. Typically used in industrial applications and for power generation, this type of switchgear is rated from 5 kV to 38 kV.
Metal-Enclosed Switchgear
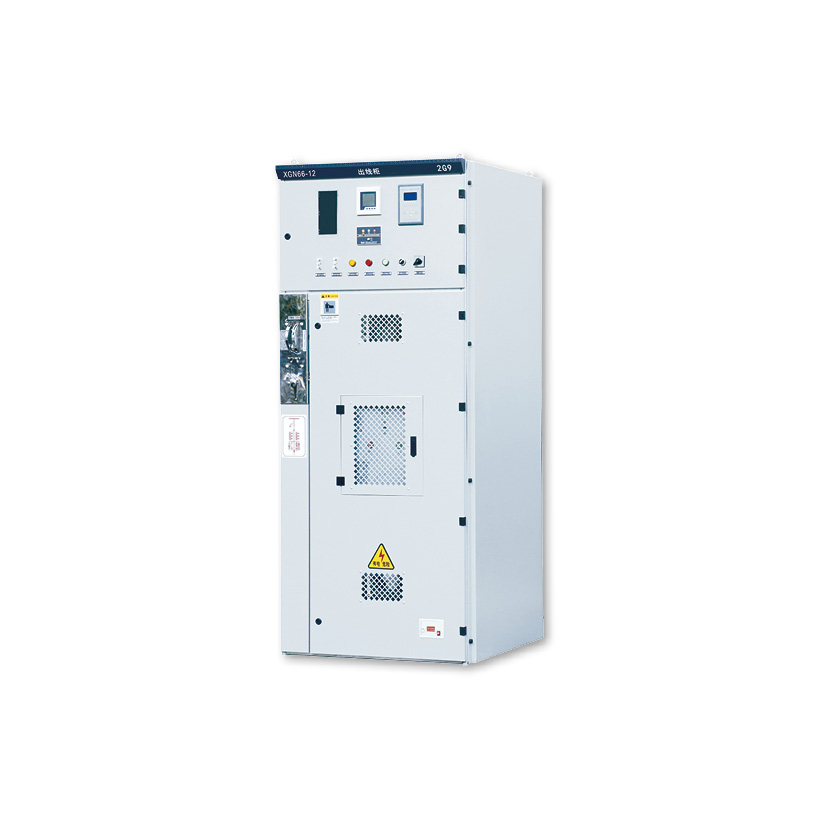
Switchgear: Defined by IEEE C37.20.3, this type of MV switchgear has all the circuit breakers in one metal enclosure and is typically used in commercial and industrial applications. This type of switchgear is typically used when the incoming electrical service is above 480/600V.
Pad-Mounted Switchgear
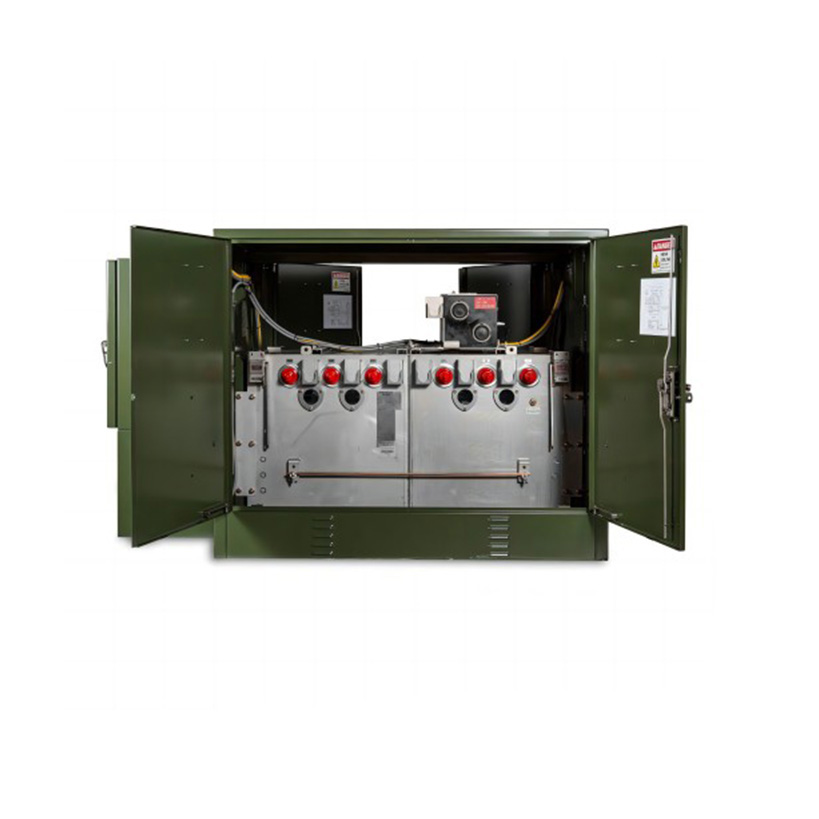
Defined by IEEE C37.74, this type of MV switchgear is designed for underground distribution systems and is operated from above ground. This type of switchgear is tamper-resistant and is typically used by utilities for distribution and circuit protection.
Vault Or Subsurface Switchgear
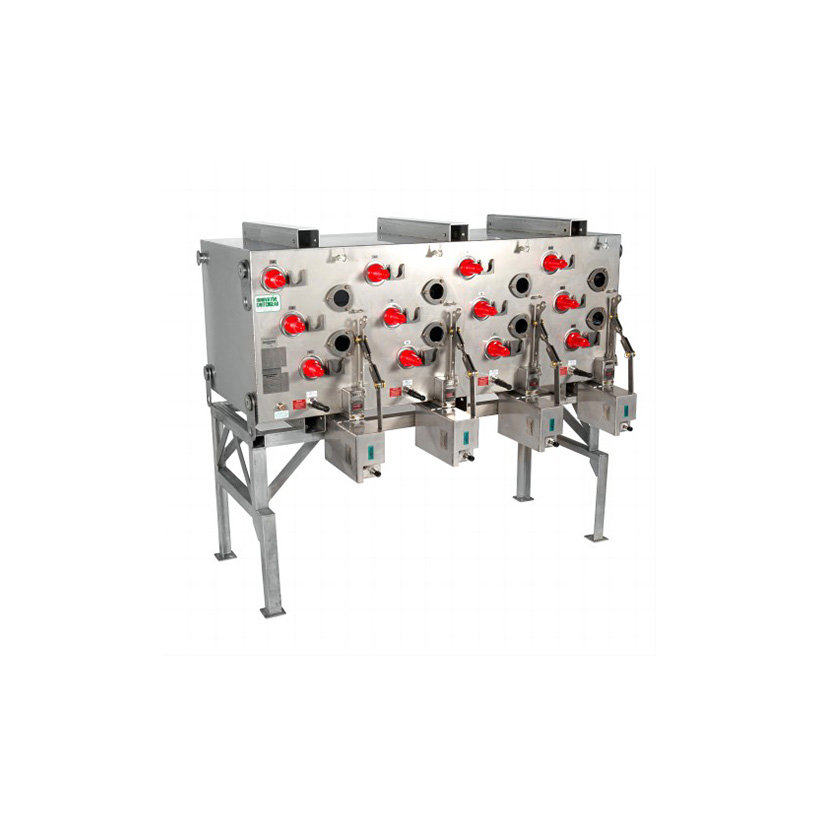
Also defined by IEEE C37.74, this type of MV switchgear is designed for use in vaults or below-grade locations that may be dry or subject to water. This type of switchgear can be manually operated or operated by relays from above ground or inside the vault.
Each type of MV switchgear is designed to meet specific operating requirements and environmental conditions, ensuring reliable power distribution and protection for various applications.
Chapter 6
Important Tests For MV Switchgear
The most important tests are listed and discussed as follows:
- Insulation resistance test
- DC or AC hi-pot test
- Power factor or dielectric loss test
- Circuit breaker contact resistance test
- Circuit breaker time-travel analysis test.
- Mechanical Operation Tests
- Temperature Rise Tests
- Short Circuit Withstand Test
- Protection Tests
- Interlock Tests
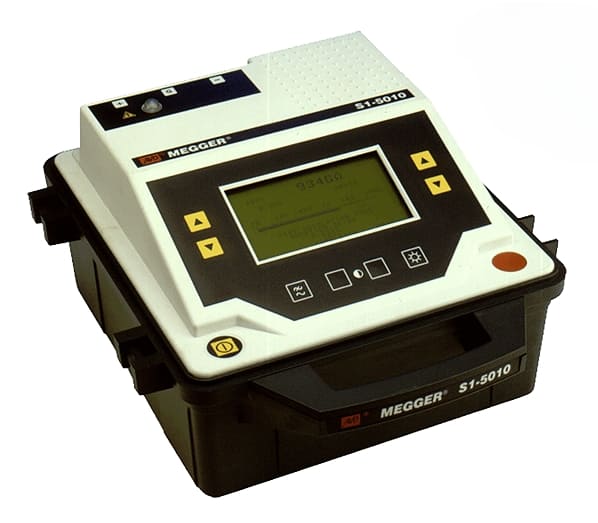
1. Insulation Resistance Testing
Insulation resistance testing is crucial for checking the condition of electrical switchgear. You usually do this test with a device called a “megohmmeter” or a “Megger.” It applies a DC voltage of 600 to 10,000 volts to the switchgear to measure the resistance in megohms. Note that it measures resistance, not the quality of the primary insulation.
What to Watch Out for When You Do Insulation Resistance Testing:
- Multiple Conductive Paths: You might get lower resistance readings because you have multiple parallel paths in the switchgear.
- Misleading High Values: A system that has a low dielectric strength can still give you high resistance readings. Use the readings to compare, not for a final determination of the quality of the insulation.
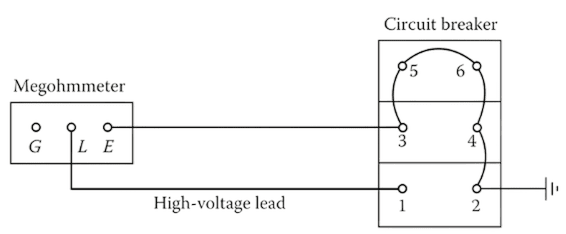
Typical connection for insulation resistance test of circuit breaker in open position
Test Setup And Procedure:
Remove the potential transformers and lightning arresters from the switchgear. This will help you avoid any issues with the test.
Detailed Testing Steps:
- Open the Circuit Breaker: Connect the high voltage (HV) lead to pole 1 and ground all other poles. Then move to pole 2, pole 3, and so on, grounding all other poles each time you move to a new pole.
- Close the Circuit Breaker: Connect the HV lead to pole 1 or 2, depending on which one is easier for you to get to. Ground the other two poles. Repeat this step for the other two phase combinations.
- Test the Stationary Gear (Buses): Connect the HV lead to phase 1 and ground phases 2 and 3. Then move to phase 2, phase 3, etc., grounding the other two phases each time you move to a new phase. Also, test the insulation resistance between the phases. For example, test between phase 1 and 2 with phase 3 grounded, and so on.
2. High-Potential (Hi-Pot) Test
DC Hi-Pot Test
DC hi-pot testing is generally not the preferred method for AC electrical switchgear due to some limitations. It is usually only used when AC hi-pot testing cannot be done.
The main challenges with DC hi-pot testing are:
- Insulation stress is different. DC voltage does not stress insulation the same way AC voltage does during normal operation, which can give you less reliable test results.
- Corona and tracking. DC voltage can cause corona discharges and tracking, especially at the sharp edges or the ends of buses. This is more of a problem on older equipment and makes it harder to use DC hi-pot testing.
If you have to do DC hi-pot testing, you want to follow the recommended voltage values for different classes of equipment that are in the specific guidelines. The procedure is the same as AC hi-pot testing to keep things consistent.
DC Hi-Pot Maintenance Test Values
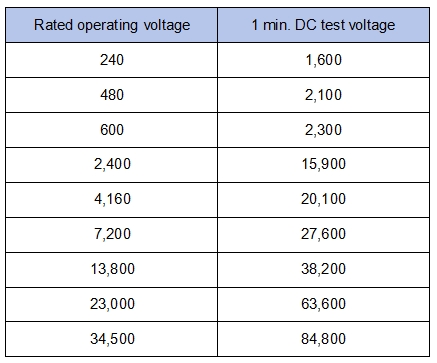
Preparation for Testing:
- Conditioning: Make sure the switchgear is cleaned up and in good shape before you test it.
- Environment Monitoring: Record the temperature and humidity and adjust your test readings.
AC Hi-Pot Test
This is the test that most closely approximates the operating conditions of AC gear and is performed after you have passed the DC Megger test and done all the necessary cleaning.
Hi-Pot Test Values
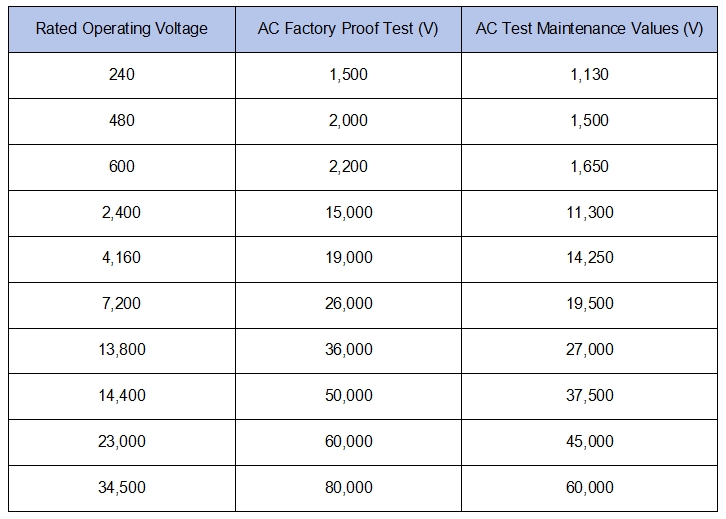
Testing Procedures:
Circuit Breakers and Buses: The AC Hi-Pot test should put the insulation in the gear under the same stress it would see in normal operation. Typically, it is run at 75% of the final factory test voltage.
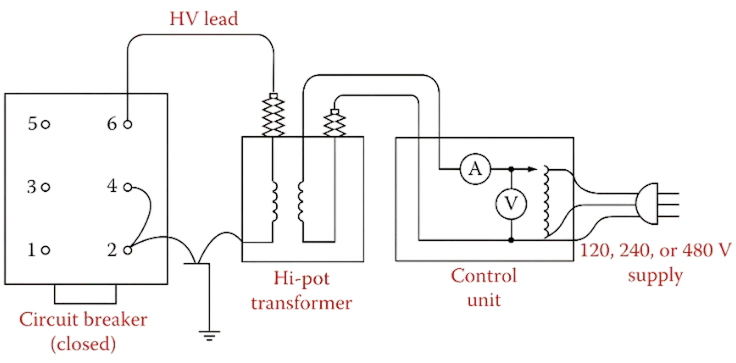
Typical connection for hi-pot test for circuit breaker in closed position
Test Setup:
- Open Circuit Breaker: Connect the HV lead to one pole at a time, ground all the others one at a time, and apply the specified high voltage per the test instructions.
- Closed Circuit Breaker: Connect the HV lead to one pole at a time and ground the other poles one at a time for each phase.
- Stationary Gear (Buses): Test by connecting the HV lead to each phase one at a time and grounding the others one at a time. Apply the specified voltage.
Once you’ve done all your repairs and cleaned everything up, the last thing you do is the hi-pot test. This is the test that tells you if everything is clean and ready to go.
3. Power Factor Testing
Power factor testing is a really important test you can do to see if your insulation is starting to go bad. You don’t care about the absolute value of the power factor, but you do care about how it changes over time.
Why Consistent Testing Conditions Matter:
You have to test the power factor at the same temperature and humidity every year to make sure you get accurate results. If the temperature and humidity change, your results will be different. So you have to adjust your test data for temperature and humidity.
Effects of Temperature and Humidity:
In general, higher temperatures and humidity levels cause power factor values to go up. Keep this in mind when you interpret your results, because these conditions can give you a higher power factor reading than you should have, which makes it look like you have more power factor deterioration than you really do.
Specific Testing Guidelines:
- Component Focus: Typically, only the air circuit breaker bushing is tested for power factor. During testing, other components, such as the arc chutes and operating rods, should be disconnected to avoid skewing the results.
- Interpreting Changes: If you see significant changes in the test results, especially increases in watts loss or the percentage of power factor, you might have an insulation problem that you should monitor more closely or investigate further.
When to Take Action:
If your power factor is less than 1%, you’re probably okay. If it’s above 1%, you have a problem.
4. Circuit Breaker Contact Resistance Measurement Test
The contacts inside circuit breakers are made of special alloys that can handle the electrical arcing. Even though they’re designed to be tough, you still need to maintain them because the electrical resistance of these contacts can go up when they arc over and over again. When the resistance goes up, the contacts can’t carry current as well. On top of that, the contacts can corrode, which makes the breaker even worse.
Testing Contact Resistance:
A good way to check the condition of breaker contacts is to do a DC test to measure the contact resistance or voltage drop across closed contacts. You should do this test from one bushing terminal to another with the breaker closed. For MV and HV systems, you should do the resistance test with a DC current of 100 amps or more because higher currents give you better results.
Measuring Resistance:
The resistance of the contacts is usually measured in microohms (µΩ). For a 15 kV class breaker, the resistance should be between 200 and 250 µΩ. There are several good microohmmeters available for this purpose.
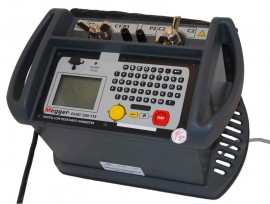
One of the most popular micro ohmmeters is the Megger DLRO 200. It can generate test currents from 10 to 200 amps. It can measure resistance from 0.1 µΩ up to 1 Ω. It is especially useful for verifying that the contacts meet their performance criteria and can help identify potential problems before they cause a failure. You need to test and maintain the contacts on a regular basis to ensure the reliability and long life of your electrical distribution system.
The Megger DLRO 200-115 High Current Digital Low Resistance Ohmmeter, 200 Amp is used to test and measure the resistance of contacts in high voltage circuit breakers, disconnecting switches (isolators), busbar joints, or for any low resistance measurement.
5. Circuit Breaker Time-Travel Analysis
Testing medium voltage (MV) and high voltage (HV) circuit breakers, especially for 34kV and above, is important to determine if there are any issues with the operating mechanism of the breaker. Most of the testing is done with electronic time-travel analyzers these days, replacing the old mechanical ones. These analyzers give you a lot of different charts and graphs that show you what’s going on with the mechanical and electrical conditions of the circuit breaker.
Here Are The Eight Tests You Can Do To A Circuit Breaker Using A Circuit Breaker Analyzer:
- Closing and Opening Time: This measures how long it takes for the contacts to close and open. This is given for each phase (e.g., 31.4 ms for phase A, 30.2 ms for phase B, and 31.8 ms for phase C).
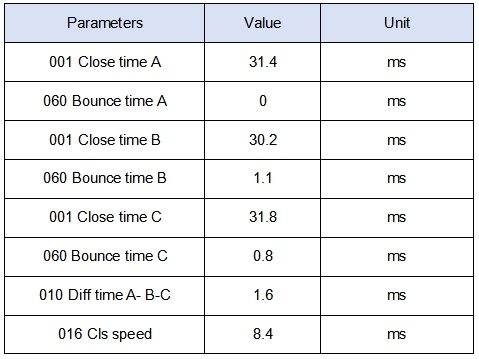
- Contact Bounce: This measures how long the contacts bounce when they’re moving. This is useful because it lets you monitor how much wear and tear is happening over time (e.g., 0.8 ms in phase C).
- Opening and Closing Synchronization: This measures how closely the contacts in each phase operate together. The maximum time difference between the fastest and slowest contacts is typically 2 ms.

- Velocity and Displacement (Speed Testing): This measures how fast the contacts move when they close and open. This is important because you need to make sure the breaker operates within safe limits.
For example, if a breaker is slow to open because it’s old or worn out, it might mess up the protection and coordination scheme of the protective relays and, as a result, cause power to go off when you don’t want it to and/or equipment to get torn up.
All breakers also have a specified closing speed. This is the average speed between two points on the motion curve.

The breaker manufacturer will give you these two points. They will tell you where to set both points to get accurate speed readings.
For example, they’ll define the first point to be set to a distance above the open position and a distance below the top point where the contact motion stops as shown below.

- Trip Operation: This is the breaker’s ability to open under fault conditions. It makes sure the mechanism has enough energy to work properly.
- Trip-Free Operation: This test checks the breaker’s ability to stay open and not reclose when you try to close it. It makes sure the breaker will work right when there’s a fault.
- Close Operation: Confirms the closing mechanism works the way it’s supposed to, within the manufacturer’s specifications.
- Trip-Close Operation: This test determines if the breaker can close again after a trip. It looks for things like bad parts or misadjustments that would make the breaker unreliable.
These tests are important during both acceptance testing and periodic maintenance, usually recommended every three years to ensure continued reliability and performance.
6. Mechanical Operation Tests
These tests make sure that the switchgear works and lasts. They check the operating mechanism to make sure it works every time over the life of the switchgear.
7. Temperature Rise Tests
This test is to make sure that the switchgear doesn’t blow up when you run rated current through it and that it doesn’t get too hot and mess up the insulation or something else.
8. Short Circuit Withstand Test
This is the big test that determines whether or not the switchgear can safely interrupt and withstand fault currents without blowing up or screwing up. It verifies that the switchgear will work when something bad happens and protect the electrical system.
9. Protection Tests
This includes testing all the protective relays and devices that are in the switchgear. It’s making sure that the relays are sensing and isolating the faults that they’re supposed to so they don’t damage the switchgear and whatever’s connected to it.
10. Interlock Tests
We test safety interlocks to make sure they work right. They’re supposed to keep you from doing something that might hurt you or break something.
Chapter 7
What Is The IEC Standard For MV Switchgear Testing?
IEC 62271-1: This standard provides the general rules for the design, testing, and performance of high-voltage switchgear and controlgear. It covers a range of equipment including circuit breakers, switchgear, disconnectors, earthing switches, and load break switches.
- IEC 62271-100: This standard is all about AC circuit breakers and tells you what you have to do to make them work, how to build them, how to test them, and how to put them in.
- IEC 62271-200 standard is all about metal-enclosed switchgear. You’ll find everything you need to know about the design, testing, and performance requirements for metal-enclosed switchgear. This standard also includes information on internal arc classification, which is really important to keep people safe if there’s an internal fault.
- IEC 62271-102: This standard tells you what you need to know about disconnectors and earth switches that you use with circuit breakers to make sure you can isolate and ground things effectively.
- IEC 62271-103: This part tells you how to build a switch that controls the flow of electricity in a high-voltage system.
- IEC 62271-105: This standard tells you how to build a switch-fuse.
- IEC 62271-110: This standard tells you how to build switchgear that can switch the kind of current you get from big motors and transformers.
- IEC 62271-111: This part is about automatic circuit reclosers and fault interrupters used in all kinds of places and ways.
Chapter 8
What Is The Difference Between LV MV And HV Switchgear?
Low voltage (LV), medium voltage (MV), and high voltage (HV) switchgear are mainly classified by the voltage level they operate at. Voltage level has a significant impact on the design, application, and safety requirements of switchgear.
Low Voltage (LV) Switchgear
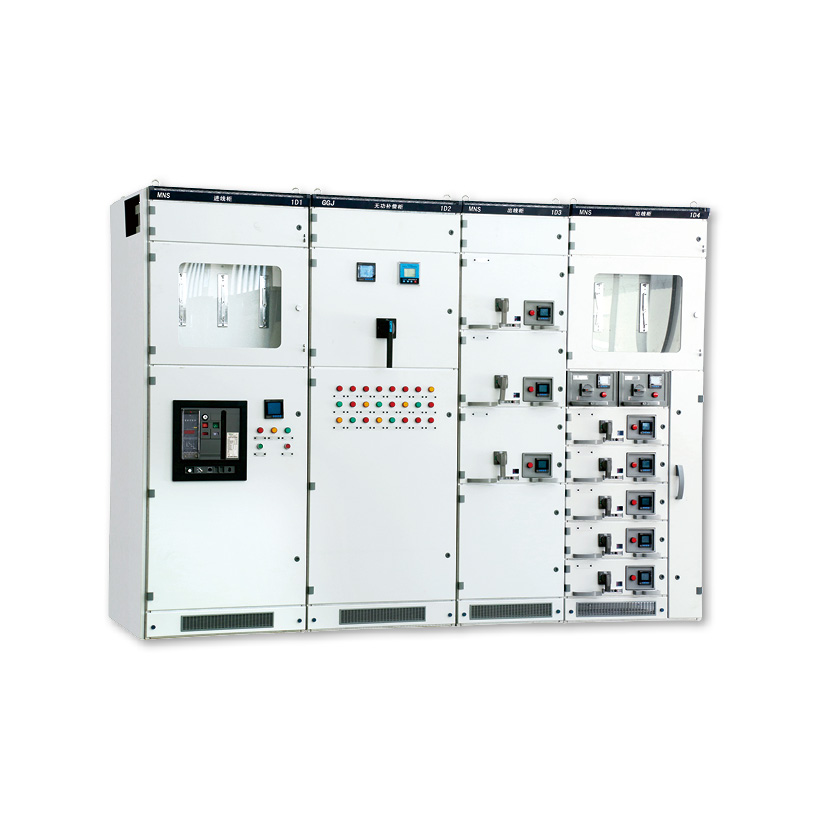
- Voltage Level: Typically up to 1,000 volts AC.
- Applications: LV switchgear is commonly used in residential, commercial, and light industrial environments. It is designed to protect and control power distribution for low voltage electrical networks.
- Components: Includes circuit breakers, switches, off-load isolators, and Earth Leakage Circuit Breaker (ELCB) devices. It often features protective relays, metering, and controls that are more simplified compared to MV and HV systems.
- Construction: Generally more compact and less complex than MV and HV switchgear, and often enclosed within metal enclosures or cabinets.
Medium Voltage (MV) Switchgear
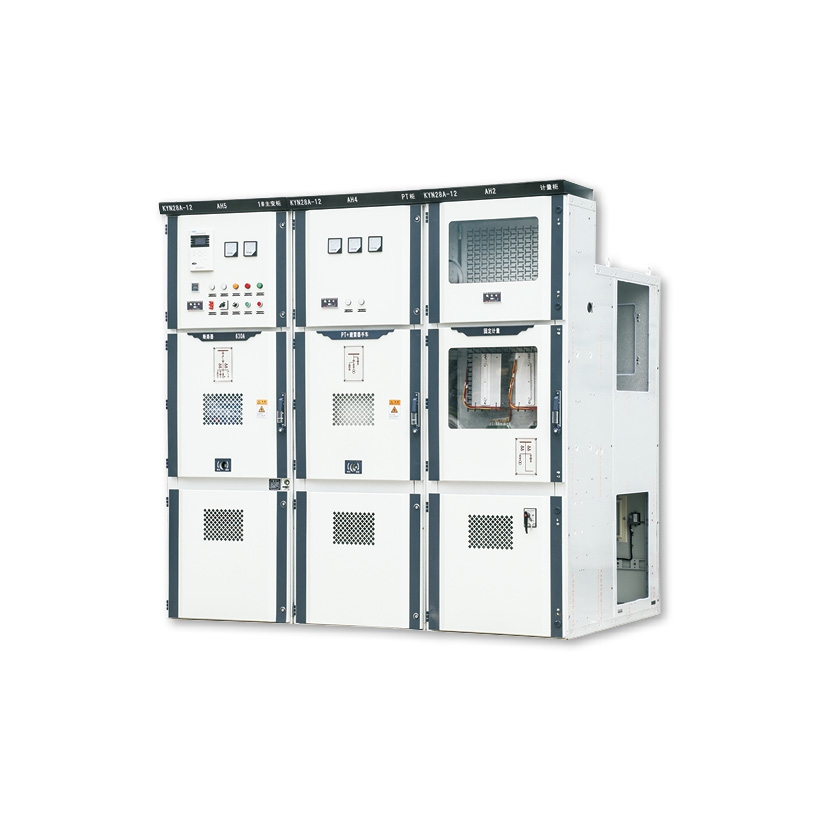
- Voltage Level: From 1,000 volts to around 36,000 volts AC.
- Applications: MV switchgear is used in industrial plants, commercial buildings, and medium-sized utilities. These are used for secondary distribution networks and in situations where space is more limited compared to high voltage facilities.
- Components: Includes vacuum circuit breakers, gas-insulated breakers, and air-insulated breakers. Protection relays are more advanced, offering features such as fault analysis and network coordination.
- Construction: MV switchgear can be metal-enclosed or metal-clad, with greater requirements for operational safety and isolation. Often, they require dedicated rooms or enclosures with controlled access.
High Voltage (HV) Switchgear
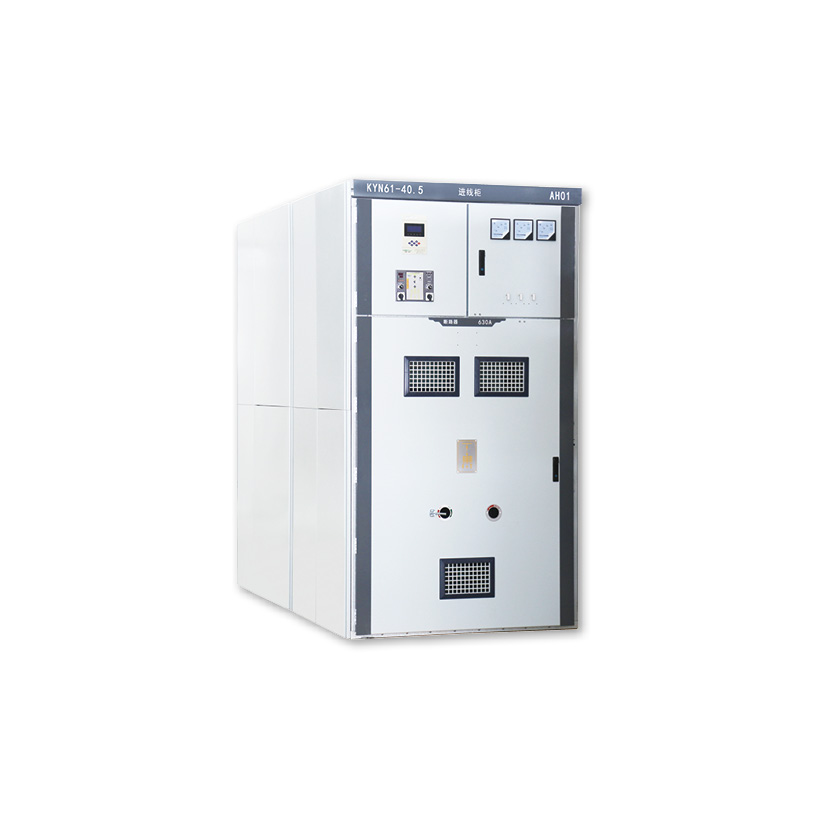
- Voltage Level: Typically from 36 kV up to 1,100 kV AC.
- Applications: HV switchgear is found in transmission networks, large-scale power generation plants, and for moving power over long distances.
- Components: HV switchgear is made up of technologies such as Gas Insulated Switchgear (GIS) and Air Insulated Switchgear (AIS) that use circuit breakers designed to handle very high voltages and currents. They have sophisticated protection and control systems that can handle complex electrical parameters and disturbances.
- Construction: HV switchgear is built tough because of the high voltages involved. It’s often in large standalone installations. It has to meet strict safety and operational protocols to keep people safe and the system reliable.
Summary
The main differences between LV, MV, and HV switchgear are their voltage ratings, which determine their applications, construction, and safety features. LV switchgear is for safer, more accessible environments. MV switchgear is a balance between accessibility and high-power handling. HV switchgear is for maximum power transmission with strict safety standards because high voltage is dangerous. All three types of switchgear are essential for different parts of the grid to make sure power gets distributed and managed efficiently, reliably, and safely.
Chapter 9
What Is The Life Expectancy Of A Medium Voltage Switchgear?
How long does medium voltage switchgear last? It depends. It depends on the quality of the switchgear, the environment it’s in, how well it’s maintained, and how often it’s used. With good maintenance, medium voltage switchgear will last 20 to 40 years.
To get the most life out of your switchgear, you need to install it right and maintain it right. That means inspecting it, testing it, cleaning it, and replacing worn parts as necessary. You also need to consider environmental conditions such as temperature, humidity, and exposure to corrosive atmospheres.
As a customer, you need to follow the manufacturer’s guidelines for maintenance and work with skilled technicians who know how to maintain medium voltage switchgear. This will keep the equipment running efficiently and safely for the life of the equipment. If you have special conditions or requirements for your installation, we can talk about those and develop maintenance and operation strategies that will work best for you.
Chapter 10
MV Switchgear Design Guide
Here’s an outline of a design guide of MV switchgear that could be helpful:
1. Understanding Medium Voltage Switchgear
- What is it? Medium voltage switchgear is a type of equipment that controls, protects, and isolates electrical equipment in the distribution system to make sure it’s reliable and safe.
- What voltage does it work at? It can work at voltages from 3000 volts up to 36,000 volts.
2. Standards And Regulations
- IEC Standards: The standard for medium-voltage switchgear up to 52 kV is IEC 62271.
- Local Regulations: Always check with local and national standards, which may vary from country to country.
3. What’s In A Medium Voltage Switchgear?
- Disconnects and Ground Switches: These are the things that make sure a part of the circuit is totally dead so you can work on it.
- Instrument Transformers: These are the things that you use to measure and relay the current and voltage.
- Protection and Control: These are the relays, meters, and control panels that manage the switchgear.
4. Design Considerations
- Safety and Accessibility: Make sure all your designs make it easy for the operator to be safe and maintain, and get in and out.
- Reliability: Use good, proven stuff so it doesn’t break.
- Scalability and Flexibility: Design it so you can add on and change it.
- Cooling and Ventilation: Make sure you get rid of the heat so it doesn’t break and lasts a long time.
- Arc Fault Containment: Make it so if it blows up, it doesn’t kill anybody.
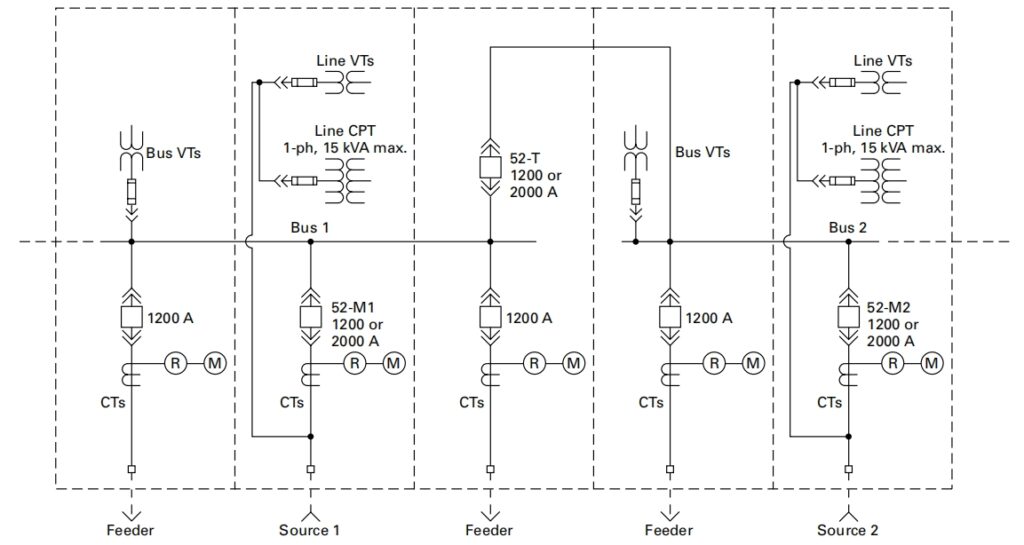
5. Switchgear Configurations
- Fixed and Withdrawable Units: Choose fixed units for compactness and cost, or withdrawable units for flexibility and ease of maintenance.
- Metal-Clad, Metal-Enclosed: Choose the type based on the application, environmental conditions, and budget.
6. Protection And Control Schemes
- Overcurrent Protection: Protection from too much current using relays and circuit breakers.
- Differential Protection: For protection from phase and earth faults.
- Control Schemes: Local and remote control options including SCADA systems for advanced monitoring and control.
7. Testing And Quality Assurance
- Routine Testing: You need to do electrical, mechanical operation, and power frequency withstand tests.
- Type Testing: You need to do dielectric tests, short circuit withstand, temperature rise, and arc resistance tests.
- Factory Acceptance Testing (FAT): Before you ship the switchgear, you need to test it to make sure it meets the design specifications.
8. Installation And Commissioning
- Installation Guidelines: Step-by-step instructions on how to get the equipment off the truck, where to put it, and how to put it together.
- Commissioning Procedures: Step-by-step instructions on how to make sure the machine is installed correctly and how to make sure it works.
9: Maintenance Practices
- Preventive Maintenance: How to keep your stuff from breaking by doing regular inspections, tests, and maintenance.
- Corrective Maintenance: What to do when your stuff breaks.
10. Documentation And Training
- Documentation: Provide detailed manuals for operation, maintenance, and troubleshooting.
- Training: Offer comprehensive training for operators and maintenance personnel to ensure safe and efficient handling of the switchgear.
Chapter 11
MV Switchgear Training
A typical medium-voltage switchgear training course will include the following topics.
1. Medium Voltage Switchgear 101
- What is switchgear?
- What are the different types of switchgear?
- What are the major components of switchgear?
2. Safety First
- Why is safety important when working with medium voltage equipment?
- What safety procedures and personal protective equipment (PPE) are required?
- What is a Lockout-Tagout (LOTO) procedure?
3. Standards And Regulations
- What are the major international standards for switchgear?
- What are the major Chinese national standards and industry regulations?
- What are the major environmental regulations?
4. Medium Voltage Switchgear Components
- What’s inside switchgear
- How the circuit breakers, isolators, earth switches, etc. work
- How to control and monitor switchgear
5. Switchgear Design And Engineering
- How to design switchgear
- How to pick the right components
- How to design for reliability, maintainability, and safety
6. Assembly And Installation
- How to put the switchgear together
- How to install and start up the switchgear
- Problems you might run into and how to fix them
7. Testing And Commissioning
- Testing before and after installation
- Type tests and special tests
- Commissioning procedures and checklists
8. Operation And Maintenance
- Daily operating procedures
- Preventive and corrective maintenance
- Troubleshooting common problems
9. Advanced Topics
- Retrofitting and modernization
- Smart switchgear and IoT
- Future trends in medium-voltage switchgear
10. Hands-On Training And Simulation
- Hands-on practice with training switchgear models
- Simulation of common operational scenarios
- Drills for emergency response and fault resolution
11. Review And Assessment
- Review of what you’ve learned
- Feedback and improvement sessions
- Certificate of completion
Appendices
- Glossary
- Further Reading
- Expert Support
Training Methodology
- Interactive Lectures: I’ll tell you what you need to know and give you examples.
- Hands-On Sessions: You’ll practice on the real thing or a simulator.
- Case Studies: We’ll look at some things that happened and work through some exercises.
- Evaluations: I’ll give you quizzes and a final exam to make sure you’re getting it.
This guide is meant to be comprehensive and can be customized to fit the specific needs and knowledge level of your team better. I recommend you update it regularly and do ongoing training to keep up with technology changes and standards and regulations.
Chapter 12
MV Switchgear Manufacturers
- High Quality, High Price: Siemens, ABB, Schneider Electric
- High Quality, Medium Price: GE Power, Mitsubishi Electric, Eaton
- High Quality, Lower Price: IE-Supply
- Medium Quality, Medium Price: CG Power, Hyosung Heavy Industries, LSIS
ABB (Asea Brown Boveri) – Based in Switzerland, ABB is a global leader in power and automation technologies that enable utility and industry customers to improve performance while lowering environmental impact. They offer a wide range of medium voltage switchgear for various applications.
Siemens AG – A German conglomerate, Siemens is one of the largest industrial manufacturing companies in Europe, with a strong portfolio in energy-efficient, resource-saving technologies including medium voltage switchgear.
Schneider Electric – Headquartered in France, Schneider Electric is a multinational company providing energy and automation digital solutions for efficiency and sustainability. They offer innovative medium voltage switchgear solutions that are widely used across industries.
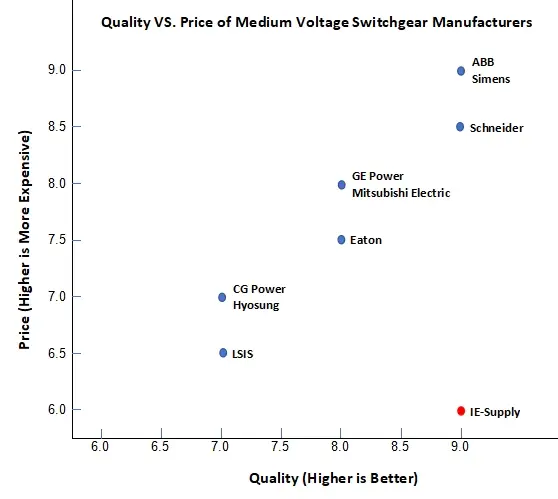
IE-Supply – Headquartered in China with a 12,000m2 manufacturing center. Russian-speaking sales both in China and Russia (Office in Moscow). ODM/OEM service can be offered. Working with ABB, CHINT, and State Grid Corporation of China, means we can guarantee the high quality of switchgear. The factory is in the center of the supply chain, which means we can provide good prices and fast delivery time.
Eaton Corporation – Based in Ireland, Eaton Corporation is a worldwide leader in diversified power management solutions that make electrical, hydraulic, and mechanical power operate more efficiently, effectively, safely, and sustainably.
GE Power (General Electric) – GE Power, a division of General Electric, is a global leader in power generation and water technologies for utilities, independent power producers, and industrial applications.
Mitsubishi Electric – Mitsubishi Electric is a multinational company that provides high-quality electrical and electronic products for a variety of industries, including medium voltage switchgear.
CG Power and Industrial Solutions – Formerly known as Crompton Greaves, this company is based in India and offers a range of power and industrial systems, including medium voltage switchgear.
Hyosung Heavy Industries – A South Korean industrial conglomerate, Hyosung manufactures high-quality medium voltage switchgear used in a variety of applications including utilities and industries.
LSIS – Formerly LG Industrial Systems, this South Korean company provides innovative solutions in the electrical power industry, including a variety of medium voltage switchgear.
- ODM/OEM Switchgear Manufacturer
IE-Supply: Customized Just for You
We design and make medium voltage switchgear, such as metal-clad switchgear, SF6 Ring Main Unit, Solid insulated switchgear, S6 gas insulated switchgear…